
David Hutchins celebrates gold anniversary as CQI member
Progress indicator

David Hutchins, CQP FCQI, Chairman and Principal at David Hutchins International, is marking 50 years as a member of the CQI, the same year the Institute celebrates its centenary. Alicia Dimas, from the CQI, talks to him about being involved with the organisation and how he discovered the benefits of the Japanese approach to quality early in his career
Alicia Dimas (AD): How does it feel having been a member for 50 years, in the 100th anniversary of the CQI?
David Hutchins (DH): One good thing about anniversaries is that they make you reflect and look back. An ambition for this year is to develop my collaborative relationship with the CQI, and hopefully the knowledge and experience I’ve gained over the years can be put to good use.
AD: Can you give me the highlights of those 50 years?
DH: When I joined in 1969, there was a lot of camaraderie between members, we all got on well, even if we were in competition with each other. Everything was run by members, and we relied much more on members volunteering to run the organisation. We got involved in the annual conference, and quite a few of us used to go to the European Organisation Quality Conferences every year, held in different cities around Europe.
I joined shortly after moving from Factory Manager in an automotive component factory to teaching at a College. I wanted to make sure that I was running the courses properly. I made the acquaintance of Brian Jenny, who was the Chairman of the Education Committee of the Institute, and he invited me to join the committee.
Becoming a CQI Fellow, in 1974, was a particular highlight for me. I was very proud to be recognised.
AD: What would you like to see for the future?
DH: I would like to see a higher profile for quality professionals in the media. It’s rare to see anyone from quality be interviewed on the news or anything like that, on why thing happen, say the Grenfell disaster. I think we could do more to get the attention of the media. The need for quality is never going to diminish and we’ve got to keep trying to progress and progress.
I would also like to see the CQI reconnected with the global quality community. I think the CQI could play a lead role in bringing all quality professionals together, for example. It wouldn’t be an easy job, but I think it could be done.
It was only later that they started to look at the management system of an organisation, as opposed to just the product as it was being produced
AD: What differences have you seen in the world of quality?
DH: In the past, quality was driven by military requirements, and it was totally inspection based until 1974. Companies were validated on their inspection systems and on the qualification or ability of the chief inspector to inspect out rubbish. It was only later that they started to look at the management system of an organisation, as opposed to just the product as it was being produced.
When I worked as Production Engineer, for a company that made high precision, high volume, pistons, piston rings and gudgeon pins for automotive and marine petrol and diesel engines, my job was to try and make sure that we didn’t make any rubbish. The Chief Inspector’s job was to try and stop whatever rubbish we did make, from getting out the door to the customer. So, my job was actually quality improvement, although we didn’t use the word quality in those days.
AD: Why is the Japanese approach to quality important to you?
DH: Back in the days when I was that production engineer in that company producing piston sets, for the automotive and marine diesel industries, I was really impressed when I analysed Japanese pistons from Honda. The grain structure was better than anything you would find, even in the British Standard for that material. There was no way we could have replicated that in our production, and it hit me: How do they do that? From that moment onwards, I desperately wanted to find out how the Japanese managed to produce quality at that sort of level.
However, I couldn’t find anything written in English – it was all in Japanese. Luckily, a few years later, a friend introduced me to Professor Ishikawa, the father of Japanese quality. Ishikawa sent me some publications written in English. There was one sentence that changed my life: “Our approach to quality is based on the idea that each person is the expert in his or her own job and our task is to use all of the skills and knowledge of all our people, to work towards making us the best in our business.”
When I read Ishikawa’s works about the workforce in Japan, I thought about those people, sitting there in front of sewing machines, all day, no self-esteem, no idea what their capabilities are. What if they could be involved in improving productivity? Improving processes? Like stop oil stains getting on the garments they are producing, or reducing the number of broken needles? This has driven me ever since.

David Hutchins has recently published his book Quality Beyond Borders
Find your membership grade
Take this short quiz to find out which CQI membership grade is right for you
Quality World
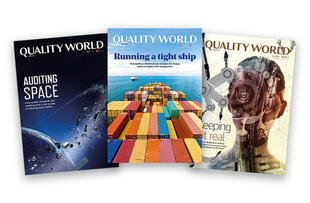
Get the latest news, interviews and features on quality in our industry leading magazine.