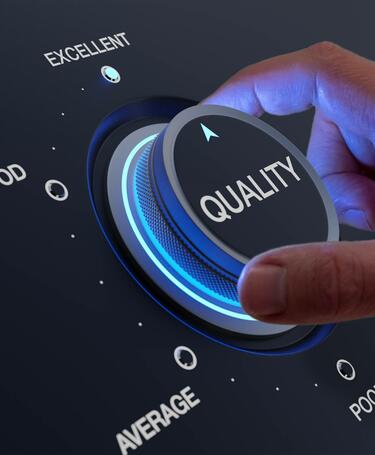
Organisational factors reducing quality standards
Progress indicator
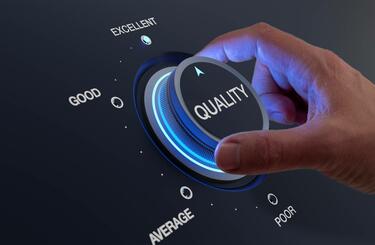
Associate auditor S Sowrirajan, Accountable Manager at Lakshmi Machine Works in India, examines the factors that can have an impact on quality standards in an organisation.
As we are all aware, quality of a product or service depends not only on the design and process, but also the human contribution in achieving it.
Humans constitute an organisation, and, within that, they frame policy, objectives and key areas under the guidance of top management, whose responsibility it is to ensure these are achieved.
Once the policies, objectives and quality assurance standards are established, it is important to measure and analyse the factors that slow down, or even downgrade, the goal of achieving the desired quality in the desired time. This analysis can also help in maintaining consistency in delivering a quality product or service. Some of the organisational factors affecting quality are:
- Insufficient infrastructure.
- Norms.
- Failure to analyse and address customer complaints.
- Not establishing quality culture throughout the organisation.
Insufficient infrastructure
Usually when an organisation is set up, there is minimal infrastructure in place at the start to achieve minimum quality standards of a product, because identifying the demand with respect to time is, as yet, unknown.
If an organisation continues with the same infrastructure for an extended period of time, quality will continue to suffer until the process is refined over time. More user-friendly and economical processes should be identified and explored as part of this process, and the infrastructure upgraded to match the demand.
"Once the policies, objectives and quality assurance standards are established, it is important to measure and analyse the factors that slow down or even downgrade the goal of achieving the desired quality in the desired time."
Following the norms
Norms are those practices followed by a group of personnel at an organisation that may not fall within quality requirements or process needs, but would definitely affect product quality. Unless the norms are identified and corrected or eliminated from time to time, the likelihood of establishing sustainable quality standards is remote.
Failure to analyse and address customer complaints
Analysing and addressing customer complaints are prime factors to establish and enhance the quality of a product. The design must satisfy the customer needs and any deficiency in it would lead to a poor quality outcome and increased customer dissatisfaction.
If an organisation wants to sustain in the market, periodical analysis of customer feedback, as well as process refinement based on customer feedback, and the requirements of the customer is a must. If this is not done, then product quality suffers.
Not establishing quality culture throughout the organisation
Establishing quality culture is essential, and it should not be limited to certain sections of an organisation. Employees in every area of a company must be quality conscious; this awareness is the foundation for developing a quality culture.
Sufficient awareness and a training programme according to the knowledge, skills and experience of employees should be carried out periodically, and it is the responsibility of top management to ensure this is done.
However, active participation of top management alone cannot establish organisational quality culture. Once a true culture of quality is in place, quality products can be produced with less supervision from senior management. Production costs, too, will be reduced because quality checks are well established at all levels.
Summary
Once an organisation has identified the destabilisers of quality and eliminated them, quality is assured. The sustainability of the product and the organisation overall will increase – a win-win situation for quality.
Read more great content from this author
"As we are all aware, aviation is a costly profession in which quality assurance plays a key role in ensuring flight safety."
Associate auditor S. Sowrirajan takes a closer look at the importance of regular audits in the highly regulated aviation maintenance sector.
CQI Mentoring
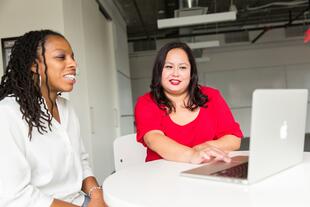
The mentoring programme has been designed to support you at different stages of your career.
Find your IRCA grade
Take our quiz to find out which auditor grade you may be eligible for