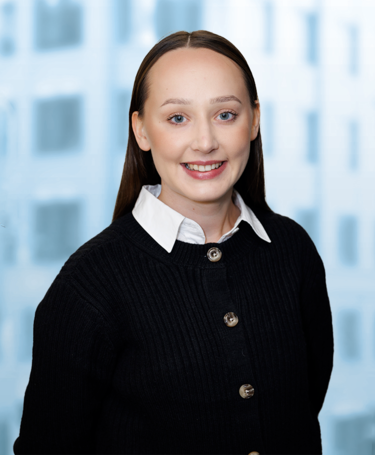
Overcoming Six Sigma scepticism
Progress indicator
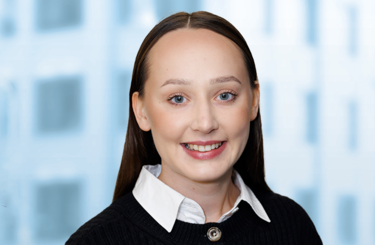
Compliance auditor Agata Kucharczyk outlines the significant benefits of employing Six Sigma methodologies, as well as ISO standards, to improve the quality of an organisation’s output.
Have you encountered businesses that harbour scepticism towards the ISO and Six Sigma methodologies when it comes to driving process improvement?
Many businesses still seem not to believe in the importance of these methodologies, perhaps because of additional cost or a lack of available resources. In my role as a Quality Assurance and Compliance Auditor, I have come to recognise that, amid economic downturns and the challenges posed by the Covid-19 pandemic, numerous businesses are hesitant to invest in quality management systems (QMS) because of cost constraints.
If more businesses embraced the principles of Six Sigma and ISO, it would not only improve their commercial situation, but also improve company reputation and customer satisfaction, as well as reduce waste and improve competency across the company.
Ensuring quality is not solely the responsibility of the quality department; it is a collective obligation of all employees. Embracing best practices can transform the dynamics and mindset within a company and foster growth. Unfortunately, this is not always easy because of a lack of time, commitment or resources. Adopting good practices would change the mentality and allow companies to grow.
"Promoting, understanding, maintaining, and introducing ISO and Six Sigma can be invaluable for organisations navigating through challenging times."
It is crucial to inspire other organisations by showcasing real examples and instilling the belief that investing in ISO or Six Sigma methodologies can yield numerous benefits. Equally important is encouraging suppliers to commit to these quality management approaches, even if it necessitates a long-term plan.
Real-life examples
The below are some real-life examples of how employing the Six Sigma methodology can reduce errors. All examples are taken from Six Sigma: A Complete Step-by-Step Guide, from the Council for Six Sigma Certification.
- According to the National Oceanic and Atmospheric Administration, air traffic controllers in the United States handle 28,537 commercial flights daily. Based on Five Sigma air traffic control, errors of some type occur in the process for handling approximately 2,426 flights every year. According to the Council for Six Sigma Certification, when Six Sigma processes are employed, that risk drops to 35.41 errors.
- The Center for Disease Control in the United States reports that approximately 51.4m surgeries are performed in the US each year. Based on a 99.97% accuracy rate, doctors would make errors in 11,976 surgeries each year – or 230 surgeries a week. When using Six Sigma, that drops to approximately 174 errors a year for the entire country, or just more than three errors each week.
- Consider an example based on Amazon shipment. On 'Cyber Monday’ in 2013, Amazon processed 36.8m orders. When using Five Sigma, Amazon experienced 8,574.4 errors – but with Six Sigma, the company only experienced 125.12 errors, resulting in significant cost savings for the business, as well as increased customer satisfaction.
Pride and success
When it comes to implementing QMS, numerous businesses often respond with statements such as "we don't need that", "our customers don't demand ISO/Six Sigma", or "we are not ready yet".
In my experience, this reluctance is often fuelled by fear of stringent requirements and additional costs. However, it is essential to not overlook the substantial benefits, including continual improvement, heightened customer satisfaction, reduced complaints, and fewer disruptions, a concept encapsulated by Deming's Plan, Do, Check, Act (PDCA) cycle.
Depending on the nature of the business, the initial investment in ISO standards and Six Sigma methodologies can yield substantial returns, fostering greater pride and success for the company.
It is truly gratifying to be part of a company that actively embraces ISO standards and adheres to other relevant laws and regulations. Witnessing the systematic processes in place that contribute to the business's growth is inspiring.
Moreover, when these processes are in place and supply chains closely collaborate with suppliers, ensuring their accreditation and conducting supply audits, it reflects a commitment to excellence This serves as a commendable example of sharing knowledge and expertise within the organisation, fostering a culture of collaboration.
Embracing good practices
While ISO standards and Six Sigma may not be mandatory, embracing them as good practices underscores the importance of remaining open to change. Sometimes, what you believe is the right thing today might change with new information.
Promoting and actively adopting ISO standards and Six Sigma methodology is crucial in reducing the costs associated with poor quality, both internally and externally. These methodologies provide valuable insights into prevention strategies and effective management of the costs of quality, ultimately contributing to enhanced organisational performance. As such, in the current economic downturn, all businesses should look for support by employing ISO standards and Six Sigma methodology.
The absence of ISO standards often leads to businesses not meeting or understanding the requirements, objectives or needs of a customer. Non-accredited companies and suppliers may also face challenges in comprehending essential elements, such as competent personnel, training protocols, traceability, control of changes, and the importance of continual improvement.
Drawing on my personal experience at a non-accredited company, understanding the customer's expectations and requirements was difficult and almost impossible to achieve. It was only after receiving training that I grasped the significance of these standards. The initial lack of knowledge and adherence to proper behaviour significantly impacted the final product. Transforming the company culture took several months, but, in my view, staying one step ahead and consistently meeting customer requirements is essential for sustained success.
Risk-based thinking is a key concept in various quality management systems, including ISO standards. Most importantly, risk-based thinking serves as a foundation for implementing strategic risk mitigation or making decisions about accepting risks at any level. Risk-based thinking can significantly influence the delivery of the project or service.
As such, employing ISO standards is not just about avoiding problems, but also about making informed decisions that contribute to achieving objectives, while understanding and managing associated risks.
Conclusion
In our collective effort to enhance quality and reduce costs, it becomes the responsibility of each one of us, as quality professionals and auditors, to actively promote awareness on a global scale. Promoting, understanding, maintaining, and introducing ISO and Six Sigma can be invaluable for organisations navigating through challenging times.
Although implementing ISO standards or adopting Six Sigma might be considered a long-term strategy, your suppliers or parental company can initiate process enhancements by gradually integrating the relevant ISO standards or embracing the methodologies of Six Sigma. By sensitively introducing non-accredited companies to these standards, and ensuring their comprehensive understanding of the requirements, we can significantly enhance supply chain quality.
I am filled with great optimism to inspire individuals and organisations to adopt and uphold robust QMS. It emphasises the importance of sharing knowledge, experiences, strategies and expertise, to ensure the creation of sustainable and consistently high-quality products or services.
How to keep success after attaining ISO 9001 certification
Achieving certification to ISO 9001 is not the end of the quality journey, says Susan Samaroo CQP MCQI.
The International Quality Awards 2024
This year's awards span eight categories, celebrating the achievements of exceptional quality professionals and auditors across the globe.
Quality World
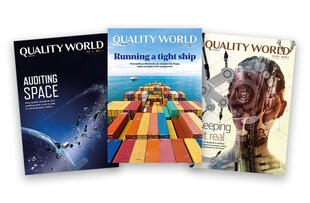
Get the latest news, interviews and features on quality in our industry leading magazine.