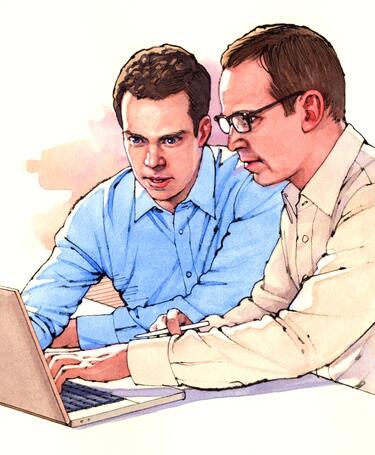
How to conduct an effective root cause analysis
Progress indicator
Mohamed Mohamedi, quality management engineer at Aramco, explains why identifying the correct root cause is crucial to recognising a valid corrective action.
The root cause is the fundamental underlying reason for a problem and if it is left unidentified the problem is likely to occur again. The problem is only fixed permanently when you have detected and taken steps to remove the root cause.
Bjørn Andersen and Tom Fagerhaug described root cause analysis in their book, ‘Root Cause Analysis: Simplified Tools and Techniques’, as “a structured investigation that aims to identify the true cause of a problem and the actions necessary to eliminate it.”
How to conduct effective root cause analysis
To conduct effective root cause analysis, quality professionals need to go through the following phases using different tools:
1. Establish the problem statement
Identify what is wrong. What are the symptoms?
2. Understand the problem
By using flowcharts, spider charts or a performance matrix.
3. Mind-map the cause of the problem
Use mind-mapping to organise your thoughts or paired comparison analysis.
4. Collect data about the problem
Use sampling and checklists.
5. Analyse the data
By using histograms, pareto charts, scatter charts or affinity diagrams.
6. Identify the root cause
By using cause and effect diagram/matrix (fishbone diagrams), the five whys or fault tree analysis.
7. Eliminate the root cause
‘Six Thinking Hats’ can help you to look at problems from different perspectives; theory of inventive problem solving (TRIZ) is a problem-solving method based on logic and data, and systematic inventive thinking (SIT)
8. Implement a solution
Using a tree diagram or force field analysis.
9. Monitor the solution.
Measuring effectiveness
How do we ensure the correct root cause has been identified and that an effective solution has been implemented? Firstly, root cause analysis results should be tested prior to defining and initiating the corrective action. This could be tested through a pre-defined approach (ie hypothesis testing/the trial experiment) to confirm if elimination of that root cause would prevent recurrence of the identified action.
Secondly, the corrective action should be verified to confirm the elimination of the root cause. This could be done through piloting the solution to test the corrective action in practice to answer any ambiguity.
Finally, the ongoing controls should be selected to ensure the root cause is eliminated. Additional controls (such as full engagement of people, measurements, ongoing control mechanisms and control charts) should be implemented as necessary when monitoring the long-term effects.
Quality professionals should bear in mind that the root cause of most problems can be traced to the lack of application of one or more of the seven quality management principles: customer focus, leadership, engagement of people, process approach, improvement, evidence-based decision making and relationship management.
Mohamed Mohamedi is an IRCA Lead Auditor (ISO 9001:2008 and ISO 9001:2015) and quality management engineer at Aramco
Member only
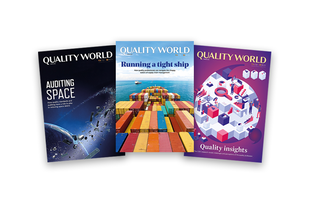
This article is free to access for a limited time only. Only CQI and IRCA members receive access to all content.
Find a course near you
Search our database of global training partners for a certified training course in a location near you.