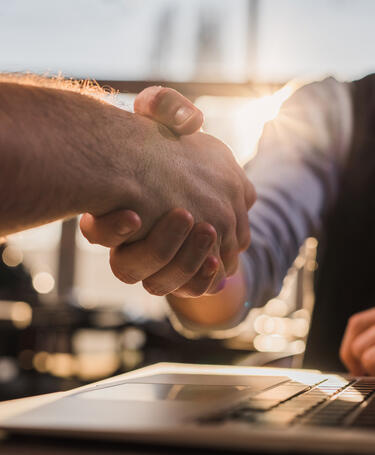
The relationship between improvement and reliability
Progress indicator
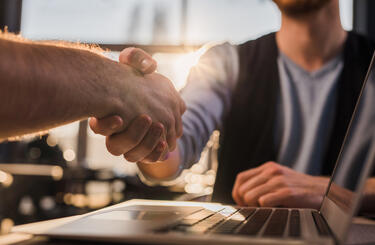
Pauline Burke, MSc PCQI, explores the role of reliability in advancing performance in operations.
With all the talk about governance, regulation, quality disasters and public scandals, it’s easy to forget that the quality profession grew out of ‘product’ quality assurance. All great thinkers in the field of quality management agree that inspection is costly, doesn't guarantee reliability and recommend improvement through a process with goals and methods. Improvement is not control, which is prevention of change, nor is assurance, which confirms product is as intended. In order for it to be effective, it must be integrated into the strategy of the organisation; it is not evolution or revolution – improvement is change.
As an engineering term, reliability has a specific meaning (see figure 1). It advances performance in operations because failures are opportunities for improvement, a reason to go back into the original plan and add some new information and experience. ISO 9001:2000 stated that improvement increases customer satisfaction and made it a permanent objective. Now, ISO 9001:2015 requires a process approach to demonstrate system effectiveness and includes the PDCA (plan, do, check, act) improvement cycle. Preventing problems is the economical and safe option as a failure could be disastrous, or as simple as customers changing suppliers. Quality planning includes product reliability and improvement, comes under Governance and contributes to customer satisfaction. In this article, the term ‘product’ includes service, agency and systems.
The science |
Reliability: The probability that a product, system or process performs its intended function for a stated period of time under specified operating conditions. Reliability is a prediction and measured using the failure rate during testing. In this way, one can calculate the mean time to failure (MTTF), mean time between failures (MTBF), mean time to repair and the average time taken to effect a repair. The time between service checks is measured in units of time, T1, T2, T3 etc, the length of which is decided by the reliability engineer or designer and failure information is normally collected at these points. |
Figure 1 |
Reliability and improvement give competitive advantage. Reliability is a factor in winning an order, it affects costs of the manufacturer over the life of the product through maintenance and warranty, and so determines price. It affects reputation, which affects new and repeat business and advertising costs. However, the client will lose confidence if the product fails. How the complaint is handled is the difference between a satisfied and a lost customer. Reliability and system efficiency build confidence and create trusting relationships.
Reliability drives improvement in managing people, equipment and sharing information. By using an improvement process to reduce defects, cycle times, waste and blockages to flow (which focuses on the elimination of waste in all forms, including time spent waiting for material or an operator), businesses achieve product reliability to the extent that inspection and testing is eliminated. It then becomes more cost effective to replace a product than to spend time testing. Many business functions contribute to product reliability and can be improved in this way (see figure 2).
Processes that contribute to product reliability and improvement |
|
Figure 2 |
The main challenge is that reliability is a prediction based on stable processes, which has to be proven. Today, there are global chains that offer identical products in their outlets. They have broken the mould for their industries by listening to the customer, and implementing stable standard processes and training.
The quality professional’s vision is a customer-focussed, value-adding, structured improvement process, linked to business enterprise and critical success factors, applying approved professional and industry standards, enabling reliable product, with top management commitment.
Reliability is jeopardised by poor governance and bad decisions based on wrong information and in a work environment where everyone is putting out fires, there is no will to develop new ideas. But when resources and information are reliable and everything is more relaxed, management can work on improving every area of the business, developing resources, benchmarking, reducing impact on the environment or contributing to the community. While fires must be extinguished and control regained, someone needs to step back and find the source of the fire.
Common tools and techniques, such as Design Failure Mode and Effect Analysis (DFMEA) and (Failure mode, effects and criticality analysis (FMECA), are used for analysis and problem-solving. But raw data does not provide meaningful information. We need clear measures to prioritise activity and to gauge whether improvement has occurred, so how information is collected, analysed and acted upon, is crucial. Surveys must be carried out personally and complaints closed out quickly.
We need clear measures to prioritise activity and to gauge whether improvement has occurred, so how information is collected, analysed and acted upon, is crucial
In conclusion, efficient, controlled, sustainable production is achievable if the management system establishes risk-aware culture, optimises its assets and meets regulatory demands, balancing long and short-term strategies, allowing the organisation to invest more in improvement. Without effective leadership, it will stagnate and in time decline.
It is in the interactions between components of the product or process that quality professionals discover what management philosophy is in operation. If it is one of harmonisation, then all the parts will work together efficiently (think of a finely tuned engine, a Swiss watch, the seasons, or a ballet). Such a system is optimised.
To embed an improvement culture, it is necessary to train the workforce so that the culture remains. We can set an example by developing our own competency and reliability within a personal development plan. It has never been easier to access information, training and journals. We need to adopt a common language by using common tools and techniques and seek ideas from employees and suppliers. When was the last time you approached a manager, team leader or supplier, just to reassure him that he's doing a good job, thank him, and ask how the relationship, process or product could be improved?
Quality World
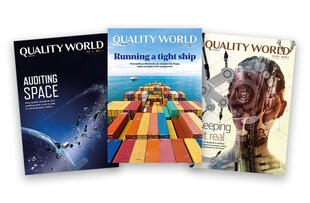
Get the latest news, interviews and features on quality in our industry leading magazine.